When planning the final flooring of a building, first you need to consider the best subfloor option as a foundation. Different subfloor materials have different pros and cons that need to be weighed.
One such subflooring option is ‘Gypcrete’. It is a cousin of concrete, except it is lighter and easier to install, but less durable and incompatible with some final flooring options.
If you feel like gypcrete is not the best option, there are plenty of substitutes that can be considered instead. Let’s see some of them.
4 GypCrete Substitutes
Here are those alternatives:
- Wooden Subflooring
- OSB Subflooring
- Concrete Subflooring
- Mixed Subflooring
In the event that gypcrete is not suitable for you as a subflooring option, you can consider the following alternatives instead.
- Wooden Subflooring
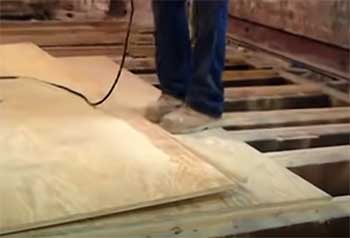
Wooden planks were a traditional subflooring option that was widely used in the past.
The traditional wooden subflooring was done by using regular 1×6 wooden planks made of softwood such as pine or fir.
The standard installation method was fitting the planks into wooden joists and then nailing them in place using regular box nails.
However, this caused the planks to loosen over time, leading to squeaky floors. Nailing the planks in place using a ring shank or fluted nails prevented this issue.
Traditional wooden subflooring was widely in practice during the mid-twentieth century and many houses built during that period still sport regular wooden subfloors.
However, since the 1950s, regular wood has largely been replaced by plywood as a standard subfloor material.
If you choose this subflooring option, you can either go for regular plywood subflooring or opt for the better tongue-and-groove plywood subflooring where the edges interlock to create a stiffer, more solid foundation.
Plywood panels for subflooring come in different thicknesses from 1/8 inches (3mm) to 3/4 inches (18mm). The thickness you use will depend on the final flooring you plan to install.
If you want carpet or vinyl flooring, thinner panels are more suitable and if you are planning to install stone or ceramic tiles, then thicker panels will be required.
- OSB Subflooring
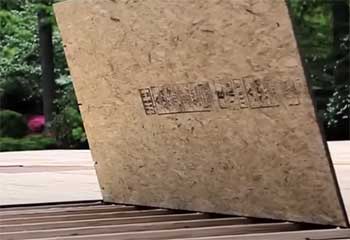
Oriented strand board or OSB is another widely used subflooring option.
OSB subflooring is very similar to plywood subflooring and is almost as commonly used.
It is even installed the same way.
On paper, OSB and plywood may appear the same, but there are certain differences between the two.
A very important characteristic to look for in a subflooring material is its water or moisture resistance, and in the case of wooden materials, its susceptibility to swelling.
Plywood is less water resistant and dries out quicker but has a greater water absorption capacity. OSB on the other hand is slightly more water resistant however, it has a higher probability to swell after getting wet.
Another important characteristic is its durability. A properly installed subfloor should last as long as the structure itself.
Compared to OSB, plywood is inherently a stiffer material with greater strength. A plywood subfloor is suitable for most kinds of final floorings from lighter carpets to heavier ceramic or stone tiles.
OSB on the other hand, while more flexible, is heavier and brittle while not being as strong as plywood. This makes OSB unsuitable for heavier floorings like stone or ceramic tiles due to the risk of getting bent or breaking.
However, it is perfectly suitable for carpets or other lighter floorings.
Last but not least, the cost plays an understandably huge role when considering subfloor materials. OSB on average costs $3 to $5 less per panel compared to plywood. A 4×8-foot sheet of plywood will set you back around $21.50, whereas a 4×8 sheet of OSB costs around $16.50.
In the end, we can conclude that plywood is the superior material for subflooring. However, if you find that the total cost is too much to bear, then OSB can prove to be a somewhat lesser but perfectly acceptable substitute for plywood.
- Concrete Subflooring
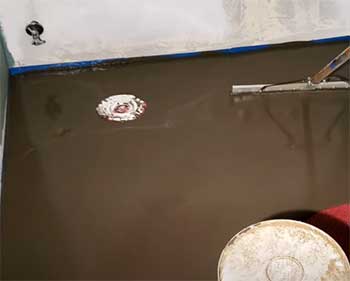
Concrete as a substance is generally very hard and strong.
If selected as a subflooring option, the concrete will be installed as individual slabs.
These slabs will ensure a strong, steady, durable, and mostly smooth foundation on which you can install finished floorings.
The average concrete slab is between 4 to 6 inches thick and weighs between 3,500-5,500 pounds per square inch. The slabs are made using water and it can take months for them to properly dry and become suitable for usage.
It is crucial to allow excess moisture to dry out from the slab before installation. Slabs that have not been dried properly before installation could cause issues down the line.
Like other subflooring materials, concrete is also susceptible to water. When exposed to excessive moisture, the foundation of concrete may weaken which can eventually lead to cracks. It can also create mold, bacteria, and algae on the concrete.
To avoid these issues, if you will be using concrete subfloors in an area prone to dampness, you should also invest in moisture barriers placed over the concrete subfloor before the final flooring installation.
When considering the final flooring options for your structure, you may come to find that one of concrete’s biggest strengths turns out to also be a weakness. Concrete, being extremely strong and durable makes for a good, solid foundation but also makes it almost impossible to nail into.
Therefore, for direct installation, concrete subfloors are only compatible with final floorings that can be glued onto the concrete. Floorings such as stone or ceramic tiles and carpets can directly be installed on a concrete subfloor.
However, if you want flooring that needs to be nailed into place, you must first install an underlayment over the concrete. Then on the underlayment, you may install your desired flooring.
- Mixed Subflooring
For your subfloor, you do not necessarily have to stick with a singular option. If you want, you have the option to use a combination of different materials to make the best subfloor for you.
An example would be to place 2-inch sleepers over concrete and then install plywood on top. This allows you to bypass concrete flooring limitations and install either glued-on or nailed-in floorings on the plywood.
Another example would be using concrete as the foundation, then laying down a floating subfloor of OSB panels that have been adhered to a layer of plastic or rigid foam. The layer acts as a moisture barrier on top of the concrete and the OSB provides a stable, flat subfloor surface ready for the final flooring.
There are many other combinations that can be explored to create the ideal subfloor for your building.
Should You Use Gypcrete As A Subfloor?
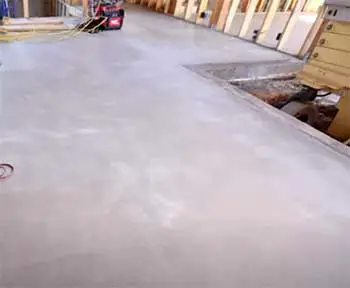
Gypcrete is most often used as a foundation in commercial and residential buildings due to being sound absorbent and fire resistant.
However, it is not suitable for industrial buildings where it will have to support heavy machinery since it cannot support as much weight as concrete.
Gypcrete also has limited flooring options that it is compatible with, making it unsuitable for many buildings.
Due to its brittle nature, gypcrete is not suitable for nail-down flooring options such as hardwood.
Its surface is also generally rough and gritty, making certain floorings difficult to install on it.
Now that we have seen all the possible substitutes, let’s talk about the material in question.
Gypcrete can be the perfect subfloor material for residential buildings or industrial complexes due to its inherent soundproof quality and fire resistance.
Or in other instances, gypcrete may prove to be entirely unsuitable due to its brittle nature and incompatibility with some floorings.
Frequently Asked Questions (FAQs)
The following are some frequently asked questions about gypcrete and their answers.
Gypcrete is a cousin to concrete and is sometimes referred to as ‘lightweight concrete’ because of its lightweight constituents which makes it lighter but less durable than concrete.
It depends on the scope of the project and the quality of the ingredients. Higher quality gypcrete will cost more than concrete. Concrete is also cheaper for covering larger areas. However, gypcrete is less expensive than pouring new concrete in smaller areas.
The minimum recommended thickness is 3/4 inches thick. In certain cases, it can be reduced to 1/2 inch thick, if reinforcement is used.
Gypcrete manufacturers only authorize licensed applicators to pour gypcrete. So, you cannot pour it yourself.
Conclusion
Every building, from commercial to residential and everything in between requires proper, stable flooring. Depending on what you need, different options are available for creating the ideal flooring.
In the end, what material you choose is entirely dependent on the specifications and requirements of the building.
And if gypcrete cannot satisfy those specifications, any of the aforementioned gypcrete alternatives will surely prove to be the right material.
You didn’t actually identify a SUBSTITUTE for gypcrete. Such a substitution would provide sound and fireproofing. Placing plywood or OSB atop a plywood subfloor does not meet the the same sound and fireproofing standard that gypcrete does.