Diamond Kote siding, manufactured by Louisiana-Pacific, is a popular choice for homeowners looking to re-side their homes. Made from treated engineered wood, Diamond Kote siding aims to provide the look and feel of traditional wood siding while requiring less maintenance.
However, some homeowners have reported problems with Diamond Kote siding warping, cracking, and deteriorating prematurely.
This article will take an in-depth look at the most common issues with Diamond Kote siding and help homeowners understand what causes these problems and how they can be prevented or repaired.
Common Problems With Diamond Kote Siding
- Fading and Discoloration
- Mold, Mildew, and Algae Growth
- Warping and Distortion
- Cracking and Splitting
- Premature Deterioration
- Problems With Timely Warranty Support
- Discontinuation Risk
Let’s talk about these issues in detail.
Fading and Discoloration
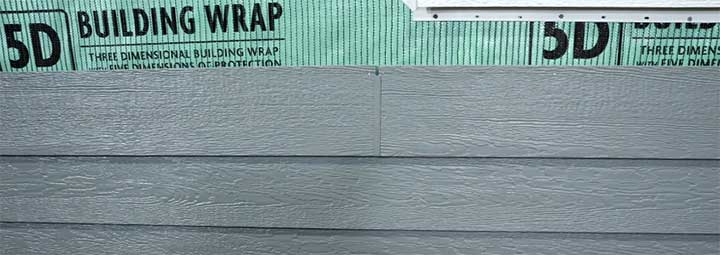
One of the most frustrating issues homeowners report with Diamond Kote siding is rapid fading and discoloration of the siding. When new, Diamond Kote has a rich, wood-like appearance.
However, within just a few years in many climates, the siding can take on a dull, faded look with graying, yellowing, or softening of the original color. This is due to a combination of factors:
- Sun exposure – Like real wood siding, the pigments in Diamond Kote can fade with prolonged exposure to UV rays. Areas facing south or west tend to be most affected.
- Heat damage – In hot climates, heat buildup on Diamond Kote siding can cause the resins and paints to break down more quickly.
- Quality of paint/stain – Lower quality paints and stains are more prone to fading and discoloration. Louisiana-Pacific frequently tweaks the formulations, so some years may be better than others.
- Improper care – Not cleaning and re-staining Diamond Kote siding at regular intervals shortens its color life span.
To minimize fading problems, experts recommend choosing darker, earthier colors that will show fading less. Providing shade with landscaping and awnings can help too. Be diligent about re-staining the siding every 3-5 years. Use high-quality exterior stains and paints specified for engineered wood.
Mold, Mildew, and Algae Growth
In damp, humid climates, many homeowners end up battling mold, mildew and algae growth on Diamond Kote siding. Just like real wood, the engineered wood substrate can accumulate moisture, dirt and organic debris, creating an environment ripe for biological growth.
Greenish-black patches of algae and milky white fungal colonies quickly spread across moist siding.
This biological growth not only looks unsightly, but it can accelerate deterioration of the siding. The microorganisms release acids as they digest the wood, compromising its integrity. Power washing alone usually isn’t enough to fully remove established growth. Instead, try:
- Controlling moisture – Improve drainage, reduce irrigation spray hitting the house, and repair leaky elements like gutters. Proper overhangs above the siding are key.
- Keeping surfaces clean – Clean siding annually with an oxygen bleach cleaner and soft brush. Avoid pressure washing.
- Using algaecide paints or primers – These contain chemicals that inhibit microbial growth on the siding.
- Applying fungicidal washes – Use these after thoroughly cleaning the siding to kill remaining spores.
With diligent moisture and cleanliness control, biological fouling can be avoided. But in chronically damp climates, vigilant maintenance will be needed.
Warping and Distortion
One of the biggest complaints about Diamond Kote siding is its susceptibility to warping and distortion issues:
- Buckling – Sections of siding can pop out and buckle away from the home. This happens when the siding gets wet and the wood substrate swells. As it dries, it can shrink back unevenly and no longer lie flush.
- Cupping – Planks can cup and warp in a curved shape. Cupping occurs when one side gets wetter than the other, causing uneven swelling and shrinkage.
- Drooping – Bottom edge of panels sag downward over time. This is caused by inadequate underlying support as the engineered wood loses structural integrity.
- Loosening – Siding planks become detached from the home. This results from improper gapping, nailing issues, or compromised integrity of the substrate.
To minimize warping and distortion problems:
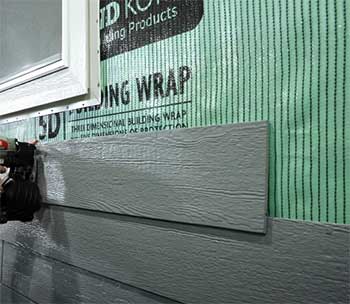
- Ensure proper gapping between siding planks and around openings to allow for expansion.
- Have an experienced siding contractor do the installation following manufacturer specifications.
- Provide adequate roof overhangs and seal any moisture entry points.
- Use quality exterior primer and paint.
- Catch problems early and re-secure any loosened planks.
With proper installation and care, Diamond Kote should remain straight and properly aligned.
But wavy or distorted areas will likely need professional repair or replacement.
Cracking and Splitting
It’s not uncommon for Diamond Kote siding planks to develop cracks and splits, often along the horizontal grain of the engineered wood boards. Contributing factors include:
- Sun damage – Prolonged UV exposure can degrade the wood fibers and protective finishes, causing brittleness.
- Freeze-thaw cycles – Repeated freezing and thawing of absorbed moisture causes expansion and contraction stress.
- Improper installation – Gaps that are too tight or nailing too close to edges restricts natural movement of the boards.
- Structural issues – Home settling or excessive wind loads can overload the integrity of the siding.
- Lower quality boards – Imperfections and less durable wood fibers create weak points.
While hairline cracks are generally just a cosmetic issue, larger splits and cracks allow moisture entry that further damages the siding. Repairs may involve:
- Sealing cracks with exterior caulk.
- Filling cracks with tinted exterior putty.
- Replacing individual cracked planks if beyond repair.
- Adding trim over damaged areas.
- Full siding replacement if cracking is widespread.
Proper installation leaving room for expansion can help minimize cracking. Inspect siding yearly and address cracks promptly to avoid bigger problems.
Premature Deterioration
Instead of lasting for decades like traditional wood siding, many homeowners report that Diamond Kote siding deteriorates prematurely, within 10-15 years. The engineered wood substrate seems prone to early breakdown, manifested in problems like:
- Soft, spongy areas – The wood fibers break down and the siding feels punky and soft when pressed on.
- Flaking – The protective paint or laminate coat peels off in flakes, leaving exposed wood underneath.
- Rotting – Excess moisture causes wood decay fungi to set in and decompose the siding from the inside out.
- Pest damage – Carpenter ants, termites, and woodpeckers are attracted to the wood-based product and can rapidly damage it.
There are a few theories as to why Diamond Kote may deteriorate prematurely:
- Improper Material Treatment – The proprietary recipe and process Louisiana Pacific uses to treat the wood fibers may result in inadequate longevity.
- Reduced Wood Quality – The composite wood fibers used may be prone to quicker breakdown.
- Moisture Damage – Even brief wetness compromises the integrity more than solid wood.
- Improper Storage and Handling – Planks are easily damaged if not handled carefully.
Unfortunately when deterioration problems appear, the only remedy is often full siding replacement. Make sure to inspect siding yearly for any signs of early breakdown. Address promptly to limit damage. Consider preventive treatments like siding washes and wood preservatives.
Problems With Timely Warranty Support
A major complaint from homeowners is the difficulty getting warranty support when problems arise with Diamond Kote siding within the warranty period. Louisiana-Pacific offers a 50 year limited warranty. However, homeowners report long delays after claims are filed, inconsistent responses, and reluctance by the company to honor the warranty.
Potential reasons for poor warranty support include:
- Volume of complaints – Widespread problems with fading, cracking, and deterioration means more claims than projected.
- Time and cost of repairs – Lengthy process for Louisiana Pacific to assess claims and determine valid defects for warranty repair.
- Ambiguity in warrant details – Vague language seems to give company leeway in denying claims.
- Company cutbacks – Louisiana Pacific has allegedly scaled back inspection and repair staffing.
- Sale to other manufacturer – The 2016 sale of LP Siding to West Fraser Timber may have complicated warranty responsibility.
Homeowners frustrated by warranty delays and denials end up having to pay out of pocket or even getting lawyers involved. Be very detailed when filing claims and persistent following up. Check if your state has helpful consumer protection laws as another recourse.
Discontinuation Risk
Another concern for Diamond Kote owners is that Louisiana Pacific reportedly plans to discontinue and stop manufacturing the product over the next few years. The company has shifted focus to its newer SmartSide line of engineered wood siding.
For current Diamond Kote owners, discontinuation creates uncertainties like:
- Replacement siding availability – Will there be enough stock to replace existing damaged siding?
- Product support – How long will installation and maintenance support continue?
- Resale value impact – Will discontinued status hurt resale value of homes sided with it?
- Warranty fulfillment – Will LP honor warranties if no longer making the siding?
There are still many unanswered questions around LP winding down Diamond Kote. But it points to the risk of discontinuation anytime you use a proprietary manufactured building product. Viable siding options with longer track records may be a safer choice for longevity.
FAQ: Common Diamond Kote Siding Questions
Diamond Kote has the attractiveness of real wood with lower maintenance needs. But it does seem prone to problems like fading, cracking, warping and deteriorating prematurely. It requires diligent upkeep and may not last as long as other sidings.
LP likely wants to shift production to its newer SmartSide line which it feels is a superior product. LP also seems to be moving away from the oriented strand board technology used in SmartSide.
While warrantied for 50 years, many homeowners report Diamond Kote deteriorating noticeably after just 10-15 years. With proper installation and maintenance, it should last at least 20-25 years in ideal conditions.
Like Diamond Kote, SmartSide has issues with premature cracking, peeling, and fungal deterioration. LP has reformulated it over the years but problems persist. It also requires meticulous moisture control.
Final Thoughts
While beautiful when first installed, Diamond Kote siding comes with inherent drawbacks like fading, mold risks in humid climates, and potential for early deterioration. Keeping the siding diligently maintained and moisture-free is key to maximizing its lifespan.
But even with proper care, issues can arise and warranty support may prove difficult. Homeowners considering siding options would be wise to fully research Diamond Kote pros and cons.
Talking to local owners about their experiences can provide valuable insights before making a decision.
HELP! We are in process of residing. Ready to ORDER Diamond Kote siding “everyone is using in our area” and “even the million plus homes use this siding” . UGH! We have twice sided our home with cement type and twice have had deterioration (crumbling edges) of siding. NOW I read this and want to cry!! What are we to do?