Crawler mounted cranes (CMC) lifts, also known as spider lifts or rough terrain cranes, are invaluable pieces of machinery for construction sites. With their ability to maneuver over uneven terrain and lift heavy loads to great heights, CMCs allow workers to efficiently hoist building materials and complete projects.
However, like any complex mechanical system, CMC lifts are susceptible to technical problems and breakdowns. In this comprehensive guide, we will explore the most common CMC lift problems contractors need to be aware of.
Knowing how to identify issues early and correct them quickly is crucial for keeping crawler cranes in service and construction projects on schedule.
Frequent CMC Lift Problems To Watch For
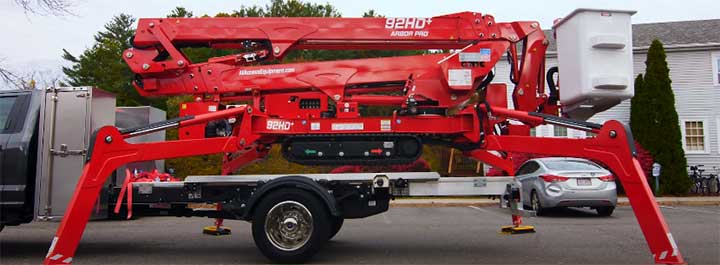
Here is a list of these issues:
- Engine Issues
- Hydraulic System Problems
- Electrical Shorts and Faults
- Structural and Mechanical Problems
- Issues with Accessories
Let’s talk about these issues in detail.
Engine Issues
The heart of any CMC lift is its powerful diesel engine. This allows the crane to generate hydraulic pressure and give the lift its lifting capacity. However, if the engine isn’t maintained properly or components begin to wear out, you may experience:
- Hard starting – If the engine cranks but won’t fire up, there could be issues with the battery, alternator, starter, or fuel system.
- Low power – A lack of engine power makes it difficult to lift loads and can indicate problems with the air filter, fuel injectors, or cylinder heads.
- Overheating – An overheating engine can warp cylinder heads and damage internal components. Check the cooling system, water pump, and radiator if temperatures run too high.
- Excessive oil consumption – Using too much oil points to leaks or engine wear that needs prompt attention.
- Smoke/misfiring – White or blue smoke, misfiring at high RPMs, and rough idling all point to fundamental engine repairs that are needed.
Regular maintenance like tune-ups, fluid changes, and inspections goes a long way to prevent major crawler crane engine repairs. Any strange noises, leaks, or performance issues shouldn’t be ignored.
Hydraulic System Problems
Hydraulics give CMC lifts their strength and allow for precision control when lifting loads. Problems with hydraulic components can completely cripple a crawler crane:
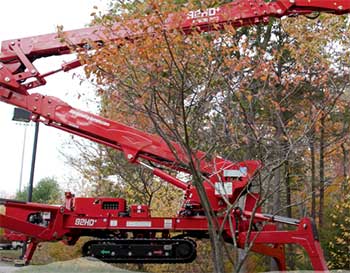
- Pressure loss – A loss of hydraulic pressure makes it impossible to lift loads or operate the boom properly. This can be caused by leaks, faulty valves, or a failing hydraulic pump.
- Jerky/inconsistent operation – If the crane’s operation seems erratic when swinging, hoisting a load, or driving, contaminated hydraulic fluid or worn components may be to blame.
- Cylinder leaks – Leaking fluid around hydraulic cylinders is a clear sign of damaged seals that must be replaced.
- Overheating hydraulic oil – Excessive heat builds up in hydraulic systems when pumps or motors are failing or there is inadequate filtration.
Preventative maintenance is crucial for hydraulic systems. Changing filters and hydraulic oil regularly, inspecting hoses/fittings for damage, and addressing leaks immediately keeps hydraulic power optimal.
Electrical Shorts and Faults
Like any specialized machine, CMC lifts contain complex electrical systems to power their lights, instruments, safety features, and operating controls. Electrical gremlins can stop a crawler crane dead in its tracks:
- Inoperable controls – If buttons, switches, and levers in the cab stop working, check for shorts and loose connections.
- Power loss – A dead battery, faulty alternator, or bad wiring can cause a total loss of electrical power during crane operation.
- Blown fuses – Short circuits and power spikes often lead to blown fuses that disable certain crane functions. Always replace with properly rated fuses.
- Faulty wiring – Damaged or corroded wires create resistance and electrical arcing. Inspect wiring with care and repair any defects.
- Instrument/sensor issues – Malfunctioning gauges, level indicators, anemometers, and load moment indicators point to deeper electrical problems.
While avoiding water exposure and damage can help, following wiring diagrams to track shorts takes time and patience. Having spare fuses, circuit testers, and electrical tools on hand aids diagnosis and repair.
Structural and Mechanical Problems
The massive steel structures and intricate mechanics of crawler mounted cranes endure tremendous stresses daily. Failure of core components can undermine safety and create costly downtime:
- Cracks in booms/frames – Supporting immense weight eventually takes a toll, leading to cracks forming in key structural members which then require immediate repair.
- Damaged/worn sheaves – Sheaves guide rope through the boom channels. Grooves in sheaves can crack or degrade, causing dangerous rope slippage.
- Leaking pistons – When hydraulic fluid seeps past seals in cylinder pistons, replacement is required to prevent bucket and arm drifting.
- Loose/broken tracks – The metal tracks distributing the crane’s weight can come loose or break, severely limiting mobility.
- Deformed outriggers – Bent outrigger arms or pads lead to unstable setups and possible tipping accidents.
Daily inspections for developing problems are vital for any crawler lift. Loose bolts, damaged guards, stuck rollers, bent components, and excessive wear will only worsen if not addressed swiftly.
Issues with Accessories
From hoist drums to counterweights, crawler cranes depend on many supplemental parts to handle loads safely. Common problems with accessories include:
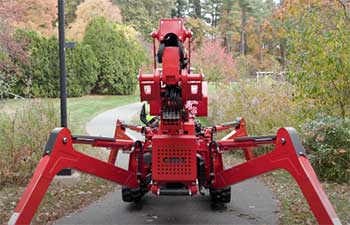
- Frayed hoist ropes – Wire rope hoist lines wear over time, requiring inspection for broken strands and replacement before they snap.
- Damaged sheaves/rollers – Sheaves and other rope guides can develop rough grooves, sharp edges, and rust damage from continual use.
- Deformed wire rope – Kinked or crushed wire rope loses strength and can fail suddenly under load. Always maintain proper unreeling and spooling.
- Leaking fuel/oil tanks – Small leaks in fuel and hydraulic tanks can lead to dangerous spills or fires if neglected.
- Dragging counterweights – Loose counterweight connections cause contact with the upper frame during slewing, requiring tightening.
- Worn tires – Insufficient tread depth on crawler tires interferes with mobility, especially in muddy or sandy conditions.
Staying vigilant about wear items like ropes, sheaves, and guards reduces the chances of catastrophic failures when lifting. Don’t overlook minor leaks or subtle damage.
How To Diagnose And Troubleshoot CMC Problems?
Now that we’ve reviewed some of the most frequent CMC lift problems, let’s discuss best practices for diagnosing and troubleshooting issues as they arise:
Perform Daily Walkaround Inspections
The first line of defense is a thorough daily walkaround to check for developing problems. Scan every system and component, looking for:
- Fluid leaks
- Unusual noises from pumps or moving parts
- Tires losing pressure or tread wear
- Frayed edges on wires and hoses
- Damage to tracks, guards, lights, mirrors, steps and handrails
- Cracks, dents, deformation, or corrosion
Document any findings to ensure necessary repairs or replacements are made promptly. Even small defects found early can prevent major failures down the road.
Monitor Instrument Readings
Dashboard gauges, load indicators, engine readouts, and other instruments provide vital clues about what’s happening internally as systems operate. Note any abnormal readings that could signal issues:
- High engine temperature
- Low fuel/oil pressure
- High hydraulic temperature
- Amp and voltage spikes
- Erratic load measurements
- Out-of-range sensor values
Compare instrument panel readings to manufacturer specifications to identify discrepancies that deserve closer inspection.
Isolate Malfunctioning Systems
When a specific problem surfaces, trace it back to the source by testing individual systems. For example, electrical faults often only affect certain crane motions, while engine issues limit power.
Isolate hydraulics, electrics, engines, and hardware until the root cause emerges. Consider renting specialized diagnostic tools to aid troubleshooting of complex systems like diesel engines. Replace components one by one until normal operation resumes.
Inspect All Potential Failure Points
Don’t assume that visible damage is the sole cause of a malfunction. Thoroughly examine every component that may contribute to the observed problem.
A “top down” approach works well – inspect wire connections, relays, motors and hydraulics feeding a damaged sheave pocket before concluding the sheave alone needs replacement. Problems often arise in multiple locations from wear and tear over time.
Leverage Operator Input
Discuss symptoms in depth with crane operators and get their perspectives on when issues began. Operators may have noticed sounds, vibrations or handling changes pointing to a certain component.
Their experience provides insights mechanics may miss. Take advantage of operator knowledge by involving them in diagnostic steps.
Seek Support When Needed
Some crawler crane problems require specialized tools, testing procedures and expertise beyond field maintenance capabilities.
If isolating an electrical short or tracing hydraulic leaks proves difficult, don’t hesitate to bring in support from the manufacturer or an experienced repair company. The right outside help can quickly pinpoint solutions and prevent wasted downtime.
Steps for Safe CMC Lift Repairs
Once the root cause of any CMC lift problem is found, proper repair procedures are essential. Here are critical steps to ensure repairs restore full function and are completed safely:
Follow Prescribed Fixes
Manufacturer service manuals, schematics, and parts catalogs provide step-by-step instructions for properly diagnosing faults and executing repairs.
Adhere closely to prescribed procedures and specifications to avoid introducing new issues. Using authorized replacement parts is also vital.
Securely Support Components
Never attempt repairs on unsupported boom sections, counterweights or other heavy components. Use slings, jacks, blocks or stands to securely support parts being serviced. Sudden movements of unsupported structures can cause serious injury.
Release Residual Pressure
Before commencing work on hydraulic or fuel systems, carefully release any pent-up pressure per manufacturer guidelines. Bleed lines, vent reservoirs, disconnect pumps, or drain systems as needed.
Lock Out Energy Sources
Battery disconnects, engine ignition switches, electrical disconnects and similar isolation methods are mandatory when performing repairs. Ensure no systems can activate unexpectedly and endanger personnel.
Use Proper Tools
Crawler crane components involve large fasteners and high torque levels. Employ properly sized tools and ensure impacts/wrenches are calibrated. Improper or damaged tool use during repairs invites further damage.
Inspect Completed Work
Prior to returning a repaired crawler crane to service, inspect all work, check fluid levels, re-secure guards and components, reconnect batteries, test operation, and follow any other manufacturer checkout procedures.
Critical safety steps can be overlooked when rushing repairs – take time to do them right.
Adhering to prescribed repair methods while following vital safety precautions ensures crawler mounted cranes are fixed properly the first time. Rushing through repairs only invites future breakdowns and risks harm to personnel or equipment.
Preventing CMC Problems with Maintenance
While even well-maintained CMC lifts experience occasional breakdowns, the most effective way to avoid major crane problems is preventative maintenance. Here are proactive crawler crane care steps to implement:
Follow Manufacturer Service Intervals
Most CMC manufacturers provide detailed maintenance schedules listing specific service tasks and intervals. Closely adhere to prescribed engine oil changes, filter replacements, fluid flushes, lubrication, adjustments, cleaning and parts inspections. Intervals range from daily to annually based on duty cycles and operating hours.
Inspect Wire Rope and Sheaves
Check wire hoist rope and boom sheaves before each use for damage, wear and proper tensioning/alignment. Lubricate wire rope regularly per specifications. Always replace rope well before recommended retirement limits. Worn sheaves also require prompt replacement.
Keep Detailed Maintenance Logs
Tracking all maintenance activities, parts replacements, fluid changes, repairs and services provides data to optimize future preventative care. Logs help determine if service intervals should be adjusted for duty cycle and highlight problem areas requiring focus.
Wash Regularly
Pressure wash crawler cranes often to remove corrosive dirt, mud and debris. Clean electrical boxes, wiring, hydraulics and moving parts give inspectors clear views during walkarounds. Avoid wetting sensitive components like electronics.
Touch Up Paint/Finish
Spot paint any scuffed or corroded areas on the crane structures before they can spread. Keep paint and finishes intact to prevent rust damage.
Lubricate Properly
Ensure all grease points are lubed as specified in manufacturer manuals. Grease pins, joints, sheaves and pivot points to prevent binding and excess wear.
Check Tire Pressures/Condition
Routinely inspect crawler crane tires for cuts, bulges and sufficient tread depth. Always keep tires inflated per specifications with high quality air compressors to ensure stability.
Make detailed maintenance logs, adhere to all service schedules, and perform thorough daily walkarounds the cornerstones of your preventative maintenance program. The time invested pays back tenfold in reduced breakdowns and safer, longer-lasting operation.
Key Takeaways on CMC Lift Problems
In summary, here are key lessons all contractors must be aware of when it comes to avoiding and correcting crawler mounted crane problems:
- Engine, hydraulic, electrical and mechanical issues are common and must be caught early. Learn symptoms of developing problems.
- Isolate issues methodically and leverage operator input during troubleshooting. Don’t assume visible damage tells the whole story.
- Strictly follow prescribed repair procedures and safety steps. Unsupported structures and pressurized systems are extremely hazardous.
- Preventative maintenance is crucial. Closely adhere to all manufacturer service recommendations and intervals.
- Inspect critical items like structural members, wire rope, and tires with vigilance. Document any abnormal findings or readings.
- Minor leaks, noises or performance changes often lead to catastrophic failures if neglected over time.
- Support repairs in the field with manufacturer documentation, proper tools, and outside expertise when needed.
- Keep detailed maintenance logs to reveal problem patterns and optimize future preventative service.
Final Thoughts
Remaining aware of potential CMC lift problems, and responding appropriately when they arise, keeps projects on track and workers safe on rugged construction sites.
Adhering to manufacturer maintenance schedules and inspecting cranes thoroughly makes preventing major crawler crane repairs possible. With sound troubleshooting procedures and preventative care, contractors can keep CMC lifts serving as indispensable lifting workhorses.